Is Your Forklift Fleet Robbing You Blind?
by Rob Budd, on May 6, 2020 6:48:49 PM
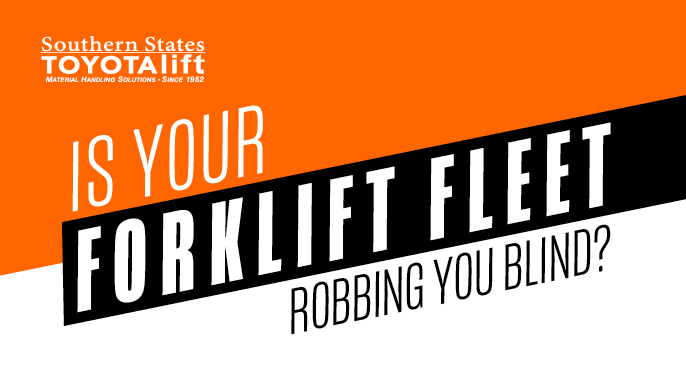
Fleet management is typically the biggest expense for a material handling operation besides payroll. Because of this, a small reduction in fleet costs can significantly improve profitability, but the reverse is also true.
Your forklift fleet may be robbing you blind in hidden ways. Here are some of the most common inefficiencies our team uncovers during a fleet assessment:
- Overspending on fleet maintenance and forklift repairs
- Using the wrong type of forklift lease
- Incorrect equipment utilization
- Too many or too few forklifts
- Underestimating cost of ownership
5 Ways to Drive Down Forklift Fleet Costs
#1 Know Your True Cost of Ownership
What do fleet managers and CFOs have in common? They’re equally surprised when we disclose the true cost of ownership for units in their fleet.A forklift purchase is typically a capital expense, but fleet maintenance expenses show up on the operational budget. “Saving money” on a forklift by choosing lower-quality equipment or skipping recommended maintenance looks good on the capital expense side, but can send cost per hour into the stratosphere. A thorough analysis of your fleet’s service records will uncover this hidden money leak. It can also tell you when to repair versus replace a forklift.
#2 Have the Correct Number of Forklifts
You can’t optimize what you’re not measuring. Supply chain managers don’t wander around their warehouse guesstimating what products need to be restocked. They use reports to make data-driven decisions. Yet, too many managers evaluate their fleets by simply looking at how many trucks are busy versus idle.
The right way to optimize your forklift fleet is by looking at fleet utilization data. A thorough analysis can tell you:
- If you have the “right-sized” fleet for your application
- Whether to keep or sell existing equipment
- Where to reallocate resources instead of acquiring new equipment
#3 Have the Correct Mix of Equipment
Fleet data analysis can also uncover areas where equipment is used for the wrong task. For example, some fleets use forklifts to move product over long distances. Tow tractors can do the same thing for a lower cost per hour (CPH) compared to forklifts.Using equipment from a variety of manufacturers can also be a financial drain. Some businesses can streamline costs by minimizing manufacturers and/or switching to a single service provider. Having one company service and track all your equipment minimizes downtime and can unlock volume discounts.
#4 Choose the Right Forklift Lease
For seasonal operations, renting a forklift during peak periods is often cheaper than buying a forklift and having it sit idle. Okay, every fleet manager knows that; but many experienced managers choose the wrong forklift lease, even though the same logic applies.Some companies significantly overspend on their “buffer” for hour overages. An organization with 10 forklifts on 2,000-hour leases may be better off with only 3 forklifts on 2,000-hour leases and 7 on cheaper, 1,000-hour contracts. Paying for a small amount of overage can end up being cheaper than buying thousands of hours you’ll never use.
Worried that your forklift fleet is robbing you blind? Schedule a consultation now.
Think you may be overspending on forklift repairs? Our new research report Short Term Savings, Long Term Losses a must-read.
#5 Don’t Overspend on Forklift Repairs
Our fleet data analysis team often finds companies drastically underestimate their forklifts’ total cost of ownership because they’re not accurately calculating forklift repair costs. In addition to acquisition and operational costs, total cost of ownership should include:
- Repair expenses
- Lost productivity while the unit is down for repairs
- Labor cost of the idle forklift operator
- Rental fees for a replacement unit (if applicable)
Multi-shift operations can sometimes lower repair costs by renting instead of purchasing forklifts. High usage also means more frequent maintenance. Ignoring regular inspections and recommended services shortens the life of your lift and significantly increases cost of ownership. When you rent a forklift from Southern States Toyotalift (SST), maintenance is included.
Knowledge, as they say, is power. At SST, our goal is to provide the information managers and executives need to eliminate waste and unnecessary spending.
Get a true picture of fleet costs and make data-driven decisions by connecting with our Fleet Management team. Send us a message online or reach us by phone at (800) 226-2345.
Further Reading:
Forklift Fleet Management - 3 Success Stories
How Short Term Savings Leads to Long Term Losses
Optimize Your Forklift Fleet and Maximize Profitability